日前,来自爱尔兰的注塑机制造商、系统解决方案提供商ENGEL宣布,将在K 2019展会上展示采用organomelt工艺生产的一种车门模块示范部件。该部件的生产单元是世界上第一个采用红外加热技术形成3种不同厚度有机板,并能在同一注塑加工阶段成型高质量可见表面的系统。该系统配备3台可同时运行的ENGEL easix关节机器人。
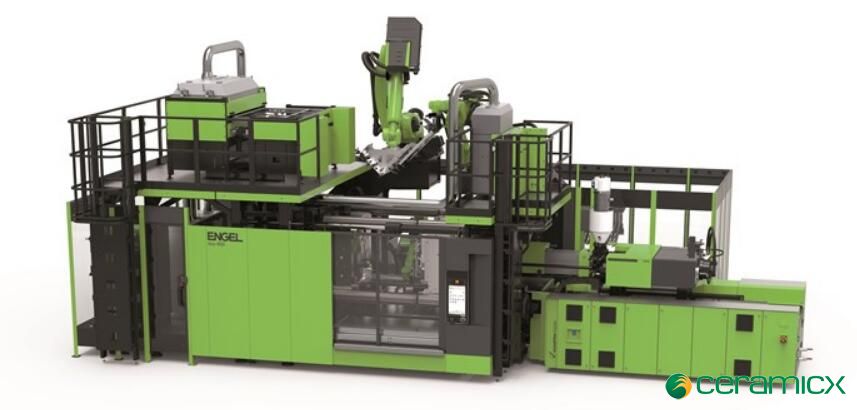
“在汽车行业的轻量化应用方面,热塑性复合材料正变得日益重要。”ENGEL轻量化复合材料技术中心负责人Norbert Müller博士表示。一方面,热塑性复合材料能将预浸料的成型性和功能化整合在一起,从而有效降低单位成本;另一方面,单纯使用热塑性聚合物更便于制定回收策略。
“在使用寿命结束时,让复合材料部件回归到材料循环中,这是电动汽车行业持续发展的首要任务之一,”Müller 表示。“热塑性复合材料解决方案应用日益广泛,甚至在飞机制造中也已开始批量化使用。”
ENGEL用organomelt工艺来满足可持续交通的发展需求。在organomelt工艺中,首先对采用热塑性的纤维增强预浸料,如有机板材和带材进行加热(红外线加热技术),然后将其放入模具中成型,接着采用热塑性塑料对其进行二次成型。这项成熟工艺已被用于大批量生产中,能够完全自动化地生产诸如前端托架之类的产品。
随着这项工艺的发展,ENGEL与其客户和合作伙伴进一步展开合作,尝试生产“拥有目标载荷分布的复合材料部件”。
“未来,将为每个部件组合使用几种不同的预浸料,以根据相关部件的形状和部件内部各区域的不同应力来定制化地开发结构部件,”Müller解释道。“将在K展展出的生产单元将清晰地展示这中应用的巨大潜力。”
该工艺是ENGEL与汽车供应商博泽合作开发的、目前世界上独一无二的集成了红外加热炉的系统,能够以自动化工艺同时加工3种不同形状、厚度的有机板材。根据博泽前期进行的各种模拟结果,在载荷分布的基础上有针对性地选用有机板材,可使部件不同部位的应力需求得到满足。
超紧凑地集成红外加热炉
加工有机板材的挑战之一是对预浸料的加热,对它们进行加热和冷却的时间取决于其厚度。因为需要将加热的预浸料快速而直接地送入模具中,因此快速加热材料而不使其受损非常重要。
organomelt生产单元基于一台duo 3660/800 注塑机,额外安装了两个集成的红外加热炉。
一个立式红外加热炉直接位于锁模单元的上方,用于加热厚度只有0.6mm的有机板材。这样,薄的有机板材几乎不费时地到达模具中,保证了成型过程中材料仍保持足够高的温度。
一个位于动模板方底座上的标准卧式红外加热炉将被用于加热1mm和2.5mm的有机板材,这种安排缩短了加热炉与模具之间的距离,节省了空间。
两个红外加热炉均由ENGEL与本地红外线加热供应商共同开发制造,它们与3台easix机器人被完整集成到注塑机的CC300控制单元中,能够通过触摸屏统一控制。
3个有机板材同时被加热,然后,3台easix机器人中的两台用于操作有机板材。它们位于锁模单位上方彼此相邻的位置,当第一台机器人负责操作两个较厚的有机板时,第二台机器人小心地操作最薄的板材。第三台机器人位于锁模单元旁边,其任务是取出成型好的部件,同时将3个有机板中的一个放入模具中以进行注塑成型。
这些有机板材是由中国原材料生产商金发提供的玻璃纤维增强聚丙烯复合材料。
当模具闭合时,有机板材即成型。
紧接着,采用玻璃纤维增强聚丙烯在同一副模具中对其进行二次成型,从而在部件的背部成型出加强筋,并在可见的一面成型出皮革纹理的外观。
“当直接对有机板进行二次成型时,我们可以获得出色的皮革纹理外观,这在以前采用有机板材时是不可能做到的,”Müller强调说。“该工作为今后采用organomelt工艺生产大型结构性的热塑性车门奠定了基础。”
红外线加热技术在未来一段相当长的时间内可帮忙许多创新型公司实现更多富有创意的产品研发制造,实现功率、效率上的双重突破。而ceramicx作为一家世界一流的红外线加热供应商,也就致力于此,与用户共同成长。